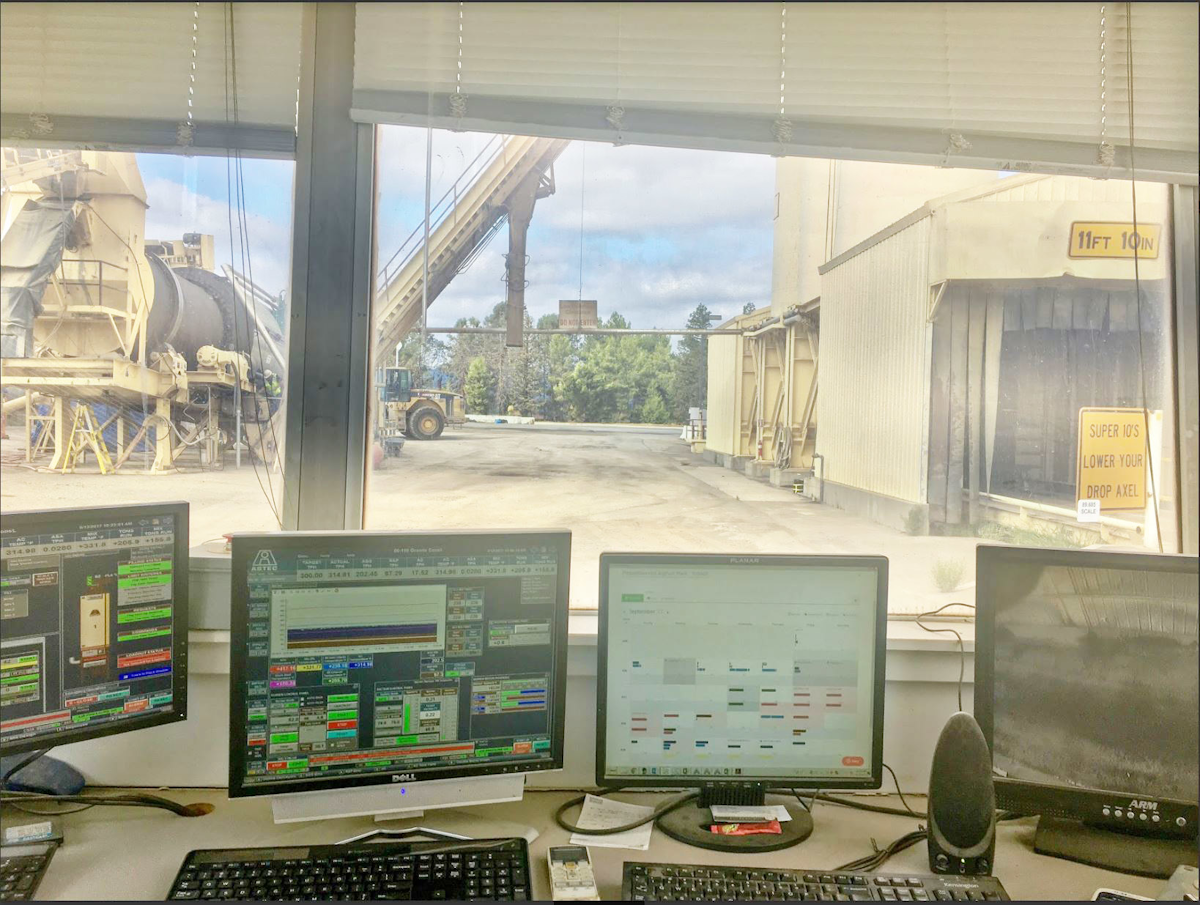
Asphalt plant owners have a lot to manage in any given day; materials, fleet capabilities, capacity, data and safety just to name a few.
This can lead to a lot of unpredictability on certain projects or with certain customers when it comes to scheduling a day. Outside events like weather, breakdowns, traffic accidents and other projects can also disrupt when a project can pave and how many tons a crew will take. Many plant operations have tried to create good ways of tracking and communicating what is coming up on the plant schedule, but this is not an easy task.
There will always be changes to when a project will go, and how much mix a paving crew will need each day. This requires communication between the paving crew and plant operations. In the past, asphalt plants have had to rely on spotty communication between all parties involved in order to try and make their best educated guess on what assets will be needed each day.
Over the years, every producer has found a way to accomplish these tasks from creating sophisticated spreadsheets to using hordes of post-it notes; often supplemented by lots of phone calls and email.
"These conversations were usually kept in someone's memory or noted on their paper notebook in the past," Daniel Mekis , continuous improvement project manager at Granite Construction and early partner with PlantDemand says. "This made it difficult to keep all of these conversations updated somewhere where everyone can see them, maybe on a shared white-board or in an excel sheet, these need to be manually updated and shared with everyone in real-time or else people will be working based on old information."
Luckily, experts in the industry have worked hard to create new tools to integrate the entire business and allow management to make informed decisions using up-to-the-minute, company-wide data.
Mix Waste & Mix Delivery Issues
Machine monitoring technology can help plant owners and operators to have a better handle on the tasks they need to manage each day and also gain a better sense of what can be done in the future to avoid catastrophic issues. One such issue is delivering the wrong mix to the wrong customer or producing the wrong mix entirely.
"With more ability to continuously monitor production by use of electronic devices, such as the mechanical metering system, the closed loop automation to verify that equipment, whether it be a liquid asphalt pump, a belt scale, or a material feed bin, is operating as instructed by the control system, the contractor/producer can be more assured that the specification is going to be met on a repeatable basis," says Gregg Gilpin, director of automation and Jeff Mitchell, director, at Stansteel/Hotmix Parts
Technology can also help ensure that the mix that is being created is 100% what the customer is expecting.
"If something is left out of the communication chain and the wrong mix is loaded, there can be serious consequences," Mekis says. "Something as “small” as producing and loading a mix with oil/bitumen from the wrong supplier - even if it is the same grade and quality - can be considered a defect, and may lead to major cost in remove & replace, or for a warranty over X years. This opens up a ton of potential risk to the contractor or plant. Most plant computers do not have the capacity to store different product supplier information or other fine details that may cause this to occur - so it is very important to be able to specify information like this so that everyone is on the same page with exactly what they plan to produce."
Producing a mix that doesn't meet customer standards not only gives your company a bad reputation, it's also detrimental to your bottom line.
"The consequences of making bad mix or the wrong mix can be costly and a nuisance or they can be extremely devastating to a producer’s reputation and financial bottom line," says Gilpin and Mitchell. "Certain older control systems actually did not have a way to quickly run the precise blend of materials and they’d have to run sometimes 15-20 tons of mix in order to make sure that the material was correct."
Gilpin and Mitchell say that some producers still will run a few tons of a mix, take a sample to their lab, have them run the extractions and gradation and then sort of tweak the settings on the plant to get it to match the outcome they want.
"Perhaps the plant called for 5.1% liquid A.C. and the mix came out at 4.5%, so they will just keep tweaking or adjusting the liquid asphalt percent up or down to get it to come out about right. This is a constant challenge to get a mix that is acceptable for the governmental unit that has specified it," they add.
Hearing the pain points of customers over the years, asphalt plant software has been developed to help plant owners and operators better manage their materials and assets from start to finish.
"Enterprise information systems integrate the entire operation, allowing the people who responsible for the data to be in control of it," Ken Cardy, president of Libra Systems says. "This allows plant operators to simply pick from pre-configured lists. These systems assist the operator by limiting the product choices to ones that have been pre-assigned for the job."
Enterprise Information Systems
These systems have been developed to help asphalt producers better improve on inefficient operations. These comprehensive system can monitors multiple points on the plant and assists the operator in making the mix according to the setpoints and getting either signal alarms in case the materials have drifted beyond a certain point or do an emergency or sequential shutdown for way out-of-tolerance mixes.
"With the AAI (Asphalt Automation Intelligence) that is built into the Accu-Track Advantage, many of these concerns that contractors have experienced have been greatly decreased," Gilpin and Mitchell say. "Since it is not just a matter of setting a device to operate at a certain level or feed a certain rate of material, there are verification devices to make sure that the equipment is operating under parameters and, in fact, is meeting the setpoints and guidelines. Stansteel was very honored to be granted a United States Patent for the Accu-Track Advantage and its unique characteristic to help the contractor make good hotmix asphalt repeatably and even change from one mix to another on-the-fly."
Silo safety systems take this one step further to help ensure that the truck is under the correct silo before dispensing the product.
"These systems are always “watching” thereby dramatically reducing the possibility of opening the wrong silo," Cardy says. "Silo safety systems are essential for any company that considers safety a priority.
In terms of mix delivery, in the past, producers have resorted to spreadsheets, or mix sheets, or other methods to be certain of what goes into each mix. But if there is not a good indicator to a plant operator of what supplier to use, the binder grade, or other factors, the communication must be at a top level. Normally an error like this is caught prior to loadout, but exactly when it is caught can be the difference in running smoothly or needing to reschedule and delay a job.
"This is where a tool like mix scheduling software can come in very handy," Mekis says. "It is specifically made for scheduling asphalt plants, and provides live information to everyone on the operational team. PlantDemand is cloud based and has iOS and Android apps, so keeping the schedule updated is much easier. Also, when there is a good calendar view where sales or dispatch can record orders (and changes to orders) further out, it gets people looking out further than just a few days or a week or two. Since it has a lot of room for specifying mix ID/names and input materials with their corresponding suppliers, it is easier to know exactly what to make and what should go in it."
Right Tech, Right Time
On top of getting the right mix out the door, if you are an asphalt plant owner that also paves, you want to make sure you're getting the mix out in timely manner. This is where having a dispatch module in place comes in handy as well.
"Sophisticated dispatch modules are available to help optimize hauling for each order," Cardy says. "When coupled with GPS, the dispatch module is an invaluable tool for maintaining proper truck spacing, not only to ensure that the paver is never held up, but also to ensure the job is not over trucked. The result is a highly profitable reduction in overall trucking costs. With truck costs of $150,000 to $180,000 per year, saving one to two trucks a day really adds up."
The dispatch modules also provide feedback on driver behavior as well as when waste is occurring during the delivery cycle.
When looking to invest in technology, make sure you're going to get exactly what you need out of it.
"Plant owners should consider tools made specifically for a task, which are simple, easy to implement, easy for their people to use, and - as we have learned in 2020 - can aid people working remotely," Mekis says. "A few years ago, several plant managers would be looking for a tool that “does it all”, but now with integration and APIs (Application Programming Interfaces) there is the capability to connect several great tools without having to wait for the unicorn to arrive. PlantDemand, truck tracking applications, Command Alkon, and other important tools have developed APIs to give the plant managers the value they desire by getting the information into a central dashboard or report.
Mekis says that it is also important that these tools are made for ease usage for the everyday busy lives of plant people. It is a common mistake for the management to focus only on their own reporting needs when selecting software, but making sure that the tools get acceptance from the team is very important for adoption and low error rates.
At the end of the day, investing in these types of technology will save your business both money and headaches down the road.
"Asset management is an important aspect of the materials business," Mekis says. "Although typically there may not seem to be a direct value to a customer’s bottom line, there is an impact to availability, sustainability/longevity of the operation and eventually a direct value to the customer."
Article From & Read More ( Asphalt Production Scheduling Tips & Tricks - ForConstructionPros.com )https://ift.tt/3j7pmtP
Tidak ada komentar:
Posting Komentar